Some of you are seasoned hands well aware of the MSHA Part 46 training requirements. But maybe a refresher would help. Others may be new to the field and might find this article a helpful introduction.
So let’s dive in and take a closer look at MSHA Part 46.
In future articles, we’ll show you how you could use minining safety e-learning courses for part of your Part 46 Training Plan, and how using a learning management system (LMS) can help you assign, deliver, track, report on, and create documentation of that training.
If you want to jump immediately to “go,” check out the following online MSHA training options and tools we’ve got for you:
- Online MSHA Part 46 New Miner and Annual Refresher Training
- Additional Online MSHA Part 46 Training Courses (New Tasks, Etc)
- Additional Online “General” Safety Training Courses
- The Convergence MSHA LMS for managing MSHA Part 46 Training, Recordkeeping, & Documentation
Finally, you’re going to be happy to know we’ve included a Free Guide to MSHA Training Requirements at the bottom of this article for you.
- Learning Management Systems for Mining Safety Training Administration
- Online MSHA Safety Training Courses
- Online Safety and Health Training Courses
- Incident Management Software
- Mobile Safety Training Apps
What Is MSHA?
MSHA is an acronym that stands for the Mine Safety and Health Administration. They’re the government agency tasked with safety and health issues at mines. One aspect of their responsibility is to make sure miners receive proper safety training.
What Is MSHA Part 46?
Part 46 is a part of CFR Title 30 Mineral Resources. It deals with mandatory training and training documentation requirements at certain mine sites (see below to learn which mines).
At Which Mine Sites Does MSHA Part 46 Apply?
Part 46 applies to “miners engaged in shell dredging, or employed at sand, gravel, surface stone, surface clay, colloidal phosphate, or surface limestone mines.” (46.1)
What Are the Training Plans and Training Programs that MSHA Part 46 Requires?
Part 46 requires operators of mines covered by the scope of Part 46 (see above) to create a “training plan” (46.3) for the mine site that includes a number of required “training programs.” In this article, we’ll explain both training plans AND training programs. We’ll look at training programs first.
What Is an MSHA Part 46 Training Program?
Part 46 requires mine operators to provide certain “training programs” to certain workers at a mine site. A training program is a set of training on specific topics (mandated by Part 46) that must be delivered to different workers and/or to workers at different times. These training programs are:
- New Miner Training Program
- Newly Hired Experienced Miner Training Program
- New Task Training Programs (one for each new task)
- Annual Refresher Training Program
- Site-Specific Hazard Awareness
We’ll go into detail about each of these in the sections below.
New Miner Training Program (46.5):
Typically, every newly hired miner who has not completed this type of training before at a different job must complete 24 hours of new miner training before that miner can work without being observed by an experienced miner. (See the definitions of New Miner and Newly Hired Experienced Miner below for more on this distinction.)
In addition, of these 24 hours, four hours must be completed before the new miner can begin work at all. After the first four hours of training have been completed, the miner can work where an experienced miner can observe that the new miner is performing his or her work in a safe and health manner until the full 24 hours of training is reached.
Let’s pause for a moment for some definitions relevant to the paragraph above. These are taken from 46.2, Definitions.
New Miner: A person who is beginning employment as a miner with a production-operator or independent contractor and who is not an experienced miner. [46.2(i)]
Experienced Miner: (i) A person who is employed as a miner on April 14, 1999; (ii) A person who has at least 12 months of cumulative surface mining or equivalent experience on or before October 2, 2000; (iii) A person who began employment as a miner after April 14, 1999, but before October 2, 2000 and who has received new miner training under §48.25 of this title or under proposed requirements published April 14, 1999, which are available from the Office of Standards, Regulations and Variances, MSHA, 1100 Wilson Blvd., Room 2352, Arlington, Virginia 22209-3939; or (iv) A person employed as a miner on or after October 2, 2000 who has completed 24 hours of new miner training under §46.5 of this part or under §48.25 of this title and who has at least 12 cumulative months of surface mining or equivalent experience. [(46.2(d)(1)(i-iv)]
Finally, there are some exceptions for miners who did work at a mine in the past, received new miner training there, but never reached “experienced miner” status. For more information on these exceptions, see 46.5(f) and 46.5(g).
When New Miner Training Must Occur | Subjects Required by New Miner Training Program |
---|---|
Before new miner begins work | 1. An introduction to the work environment. Includes a visit and tour of the mine, or portions of the mine that are representative of the entire mine (walk-around training). The method of mining or operation utilized must be explained and observed. |
Before new miner begins work | 2. Instruction on the recognition and avoidance of electrical hazards and other hazards present at the mine. Instruction can include things such as traffic patterns and control, mobile equipment (e.g., haul trucks and front-end loaders), and loose or unstable ground conditions. |
Before new miner begins work | 3. A review of the emergency medical procedures, escape and emergency evacuation plans, in effect at the mine, and instruction on the fire-warning signals and firefighting procedures. |
Before new miner begins work | 4. Instruction on the health and safety aspects of the tasks to be assigned. Includes the safe work procedures of such tasks, the mandatory health and safety standards pertinent to such tasks, information about the physical and health hazards of chemicals in the miner’s work area, the protective measures a miner can take against these hazards, and the contents of the mine’s HazCom program. |
Before new miner begins work | 5. Instruction on the statutory rights of miners and their representatives under the Act. Instruction should be based on the Federal Mine Safety & Health Act of 1977. |
Before new miner begins work | 6. A review and description of the line of authority of supervisors and miners’ representatives and the responsibilities of such supervisors and miners’ representatives. |
Before new miner begins work | 7. An introduction to your rules and procedures for reporting hazards. |
Before new miner begins work | 8. Site-specific hazards. Note: Part 46 doesn’t specifically call out training on “site-specific hazards” in the same way that it does the other topics listed above (or below), but instead notes that the training topics listed above “must also address site-specific hazards.” As a result, we’ve chosen to call them out specifically so it’s less likely you’ll miss this. |
No later than 60 calendar days after a new miner begins work at the mine | 9. Instruction and demonstration on the use, care, and maintenance of self-rescue and respiratory devices, if used at the mine. |
No later than 60 calendar days after a new miner begins work at the mine | 10. A review of first aid methods. |
No later than 90 calendar days after a new miner begins work at the mine | 11. The balance, if any, of the 24 hours of training on any other subjects that promote occupational health and safety for miners at the mine. |
You may also want to see this article for more on MSHA Part 46 New Miner Training Requirements.
And here’s a helfpul article about online training options for MSHA Part 46 New Miner training.
Newly Hired Experienced Miner Training Program (46.6):
Newly hired experienced miners (remember the definition of “experienced miners” above) must receive a different training program than newly hired (non-experienced) miners do. The two training programs are similar and there’s overlap, but in general, newly hired experienced miners have to complete less training than new miners do.
Some of this training must be completed before the newly hired experienced miner can begin work. The rest of it must be completed within the first 60 days. There’s a partial exception for an experienced miner “…who returns to the same mine, following an absence of 12 months or less…”–see 46.6(f) for the details.
Newly hired experienced miners must receive no less than four hours of training on the subjects numbered 1-8 below before they begin work at the mine.
In addition, they must receive training about self-rescue and respiratory devices, if used at the mine, no later than 60 days after beginning work.
It’s all explained in detail in the table below.
When Newly Hired Experienced Miner Training Must Occur | Subjects Required by Newly Hired Experienced Miner Training Program |
---|---|
Before new miner begins work | 1. An introduction to the work environment. Includes a visit and tour of the mine, or portions of the mine that are representative of the entire mine (walk-around training). The method of mining or operation utilized must be explained and observed. |
Before new miner begins work | 2. Instruction on the recognition and avoidance of electrical hazards and other hazards present at the mine. Instruction can include things such as traffic patterns and control, mobile equipment (e.g., haul trucks and front-end loaders), and loose or unstable ground conditions. |
Before new miner begins work | 3. A review of the emergency medical procedures, escape and emergency evacuation plans, in effect at the mine, and instruction on the fire-warning signals and firefighting procedures. |
Before new miner begins work | 4. Instruction on the health and safety aspects of the tasks to be assigned. Includes the safe work procedures of such tasks, the mandatory health and safety standards pertinent to such tasks, information about the physical and health hazards of chemicals in the miner’s work area, the protective measures a miner can take against these hazards, and the contents of the mine’s HazCom program.Note: According to 46.4(d), “Practice under the close observation of a competent person may be used to fulfill the requirement for training on the health and safety aspects of an assigned task in paragraph (b)(4) of this section, if hazard recognition training specific to the assigned task is given before the miner performs the task.” |
Before new miner begins work | 5. Instruction on the statutory rights of miners and their representatives under the Act. Instruction should be based on the Federal Mine Safety & Health Act of 1977. |
Before new miner begins work | 6. A review and description of the line of authority of supervisors and miners’ representatives and the responsibilities of such supervisors and miners’ representatives. |
Before new miner begins work | 7. An introduction to your rules and procedures for reporting hazards. |
Before new miner begins work | 8. Site-specific hazards. Note: Part 46 doesn’t specifically call out training on “site-specific hazards” in the same way that it does the other topics listed above (or below), but instead notes that the training topics listed above “must also address site-specific hazards.” As a result, we’ve chosen to call them out specifically so it’s less likely you’ll miss this. |
No later than 60 calendar days after a new miner begins work at the mine | 9. Instruction and demonstration on the use, care, and maintenance of self-rescue and respiratory devices, if used at the mine. |
Various “New Task” Training Programs (46.7):
A miner must be complete a “New Task” Training Program every time the miner “is reassigned to a new task in which he or she has no previous work experience.” This training must be completed before the miner can begin the new task. In addition, the miner must receive similar safety training “If a change occurs in a miner’s assigned task that affects the health and safety risks encountered by the miner.”
Again, let’s pause for a definition from the regulation:
Task: a work assignment or component of a job that requires specific job knowledge or experience. [46.2(n)]
So, for example, you might have New Task Training programs like the ones listed below (and obviously, there could be many more).
- Dozer Operator
- Haul Truck Operator
- Welding
- Operating a Crusher
According to part 46.7, the training must include “the health and safety aspects of the task to be assigned, including the safe work procedures of such task, information about the physical and health hazards of chemicals in the miner’s work area, the protective measures a miner can take against these hazards, and the contents of the mine’s HazCom program. ”
There’s an exception for miners “who have received training in a similar task or who have previous work experience in the task. ” These miners must “demonstrate the necessary skills to perform the task in a safe and healthful manner.” See 46.7(c) for more details.
You may also want to check this article for more information about using online training for MSHA Part 46 New Task training.
Annual Refresher Training Program (46.8):
Once you’ve provided your “new hire” miners with the New Miner Training Program or the Newly Hired Experienced Miner Training Program, and you’ve delivered any New Task Training Programs necessary, the next thing to do is to turn your attention to the Part 46 requirement for Annual Refresher safety and health training.
All miners must receive eight hours of annual refresher training. This training must be provided “No later than 12 months after the miner begins work at the mine” and “Thereafter, no later than 12 months after the previous annual refresher training was completed.” (46.8)
Again, let’s take a look at a key definition here from 46.2.
Miner: (i) Any person, including any operator or supervisor, who works at a mine and who is engaged in mining operations. This definition includes independent contractors and employees of independent contractors who are engaged in mining operations; and (ii) Any construction worker who is exposed to hazards of mining operations.
The standard goes on to say that “The definition of “miner” does not include scientific workers; delivery workers; customers (including commercial over-the-road truck drivers); vendors; or visitors. This definition also does not include maintenance or service workers who do not work at a mine site for frequent or extended periods.”
This training can include repeats of the training that was provided as part of the New Miner and the Newly Hired Experienced Miner Training Programs. We’ve covered that above, so we won’t go into detail about that here.
In addition, however, 46.8 says two things that are of particular interest here.
First, the standard says that you “must include instruction on changes at the mine that could adversely affect the miner’s health or safety.”
And second, the standard lists some additional topics for which you could provide annual refresher training. This list is informative, so we’ll copy a rather large section of the standard here [46.8(2)(c)]:
“Refresher training must also address other health and safety subjects that are relevant to mining operations at the mine. Recommended subjects include, but are not limited to: applicable health and safety requirements, including mandatory health and safety standards; information about the physical and health hazards of chemicals in the miner’s work area, the protective measures a miner can take against these hazards, and the contents of the mine’s HazCom program; transportation controls and communication systems; escape and emergency evacuation plans, firewarning and firefighting; ground conditions and control; traffic patterns and control; working in areas of highwalls; water hazards, pits, and spoil banks; illumination and night work; first aid; electrical hazards; prevention of accidents; health; explosives; and respiratory devices. Training is also recommended on the hazards associated with the equipment that has accounted for the most fatalities and serious injuries at the mines covered by this rule, including: mobile equipment (haulage and service trucks, front-end loaders and tractors); conveyor systems; cranes; crushers; excavators; and dredges. Other recommended subjects include: maintenance and repair (use of hand tools and welding equipment); material handling; fall prevention and protection; and working around moving objects (machine guarding).”
Site-Specific Hazard Awareness Training Program (46.11):
According to 46.11(d), “Site-specific hazard awareness training is information or instructions on the hazards a person could be exposed to while at the mine, as well as applicable emergency procedures.”
The training requirements for site-specific hazard awareness training apply to two large groups of people:
First, the miners performing miner operations. In most cases, this site-specific hazard awareness training would be provided initially as part of the New Miner Training Program or the Newly Hired Experienced Miner Training Program. In addition, it could be covered in various New Task Training Programs (which can be included in the previous two). And finally it might be included in the yearly Annual Refresher Training Program.
Second, it must be provided “to any person who is not a miner as defined by §46.2 of this part but is present at a mine site.”
All together, that means mine operators must provide site-specific hazard awareness training to the following people [46.11(a, b, and c)]:
- Newly hired miners and experienced miners, as defined above. This training can be part of their new miner and newly hired experienced miner training programs.
- Miners, such as drillers or blasters, who move from one mine to another mine while remaining employed by the same production-operator or independent contractor (provide site-specific hazard awareness training for each mine)
- Office or staff personnel
- Scientific workers
- Delivery workers
- Customers, including commercial over-the-road truck drivers
- Construction workers or employees of independent contractors who are not miners under §46.2 of this part
- Maintenance or service workers who do not work at the mine site for frequent or extended periods
- Vendors or visitors
Who’s NOT required to receive and complete site-specific hazard awareness training? According to 46.11(f), “Site-specific hazard awareness training is not required for any person who is accompanied at all times by an experienced miner who is familiar with hazards specific to the mine site.”
In terms of the training topics/subjects to be covered, the standard has this to say:
“Information or instructions on the hazards a person could be exposed to while at the mine, as well as applicable emergency procedures. The training must address site-specific health and safety risks, such as unique geologic or environmental conditions, recognition and avoidance of hazards such as electrical and powered-haulage hazards, traffic patterns and control, and restricted areas; and warning and evacuation signals, evacuation and emergency procedures, or other special safety procedures.”
What Is an MSHA Part 46 “Training Plan?”
So we’ve now covered the 5 “basic” Part 46 Training Programs. To refresh, they are New Miner, Newly Hired Experienced Miner, Annual Refresher, Site-Specific Hazard Awareness, and any number of New Tasks.
Now let’s take a step back and learn about what Part 46 calls a Training Plan (46.3 and 46.4).
A Training Plan is “a written plan…that contains effective programs for training new miners and newly hired experienced miners, training miners for new tasks, annual refresher training, and site-specific hazard awareness training.” [46.3(a)] Mine operators regulated by Part 46 must develop an implement a Training Plan.
What Must a Training Plan Include?
The Training Plan is a written plan for delivering your various Part 46 training programs. According to 46.3(b), here’s what your Training Plan has to include (at minimum):
- “The name of the production-operator or independent contractor, mine name(s), and MSHA mine identification number(s) or independent contractor identification number(s)” [46.3(b)(1)]
- “The name and position of the person designated by you who is responsible for the health and safety training at the mine. This person may be the production-operator or independent contractor” [46.3(b)(2)]
- “A general description of the teaching methods and the course materials that are to be used in the training program, including the subject areas to be covered and the approximate time or range of time to be spent on each subject area” [46.3(b)(3)]
- “A list of the persons and/or organizations who will provide the training, and the subject areas in which each person and/or organization is competent to instruct” [46.3(b)(4)]
- “The evaluation procedures used to determine the effectiveness of training” [46.3(b)(5)]
Do You Have to Submit Your Part 46 Training Plan to MSHA?
Typically, you don’t have to submit your Part 46 Training Plan to MSHA. Note that 46.3(a) says just that “You must develop and implement a written plan…” and that the plan is “considered approved” if it includes the elements listed above and in 46.3(b).
However, you CAN “voluntarily submit a plan for Regional Manager approval” if you want [see 46.3(c) for more about this].
Also, if your Training Plan DOES NOT include the items listed in the section above [taken from 46.3(b)(1-5)], then you’ll HAVE TO submit your Plan to your MSHA Regional Manager for approval. Here’s what the standard says: “A plan that does not include the minimum information specified in paragraphs (b)(1) through (b)(5) of this section must be submitted to and approved by the Regional Manager, Educational Field Services Division, or designee, for the region in which the mine is located.”
Submitting Your Training Plan to the Miner’s Representative
You must ALWAYS submit a copy of your Training Plan to your miners’ representative, if any, “at least 2 weeks before the plan is implemented” [46.3(d)]. In addition, IF you intend to submit your Training Plan to MSHA for approval, you must make the plan available to the miner’s representative “at least two weeks before you submit the plan to the Regional Manager for approval” [46.3(d)].
If the mine has no miner’s representative, “you must post a copy of the plan at the mine or provide a copy to each miner at least 2 weeks before you implement the plan or submit it to the Regional Manager for approval.”
After you’ve made the plan available to miners and/or their representative, know that “within 2 weeks following the receipt or posting of the training plan under paragraph (d) of this section, miners or their representatives may submit written comments on the plan to you, or to the Regional Manager, as appropriate” [46.3(d)].
Finally, if you DO submit your plan to MSHA and they approve it, “you must provide the miners’ representative, if any, with a copy of the approved plan within one week after approval. At mines where no miners’ representative has been designated, you must post a copy of the plan at the mine or provide a copy to each miner within one week after approval” [46.3(d)].
Keeping Training Plan Available for Inspection by MSHA, Miners, and/or Miner’s Representative
Here’s what you’ve got to know about keeping your Training Plan available for inspection:
“You must make available at the mine a copy of the current training plan for inspection by us and for examination by miners and their representatives. If the training plan is not maintained at the mine, you must have the capability to provide the plan within one business day upon request by us, miners, or their representatives.” [46.3(i)]
Implementing Your MSHA Part 46 Training Plan
Having a Training Plan is great. First, because you’re required to. But second, because it’s good to have a plan for your mine safety training.
But having a plan is only the first part of the solution. The second part is to put that plan into action. You’ve got to deliver the safety training to your workers–and that’s what Part 46 means by “implementing the plan,” which is what 46.4 is all about.
When you provide the training, you’ve got to ensure that it’s:
- Conducted in according with the written training plan
- Presented by a competent person
- Presented in a language that the miners who are receiving the training understand.
- Before we go further, let’s backtrack a bit (within Part 46, that is) and make sure we know the definition of “competent person.”
Competent Person: “a person designated by the production-operator or independent contractor who has the ability, training, knowledge, or experience to provide training to miners in his or her area of expertise. The competent person must be able both to effectively communicate the training subject to miners and to evaluate whether the training given to miners is effective.” (46.2, Definitions)
Who Can Conduct the MSHA Part 46 Training?
You can conduct your own training, but you don’t have to.
Here’s what Part 46 has to say:
“You may conduct your own training programs or may arrange for training to be conducted by: state or federal agencies; associations of production-operators or independent contractors; miners’ representatives; consultants; manufacturers’ representatives; private associations; educational institutions; or other training providers.” [46.4(b)]
You may also want to check out these articles for more about the MSHA Part 46 Competent Person role and the MSHA-Approved Instructor Role (which is relevant for MSHA Part 48).
What Training Methods Can You Use for MSHA Part 46?
MSHA places few, if any, restrictions on you for the training method you use to deliver your Part 46 training.
In their own words:
“Training methods may consist of classroom instruction, instruction at the mine, interactive computer-based instruction or other innovative training methods, alternative training technologies, or any combination of training methods.” [46.4(c)]
You may also want to read this article demonstrating that online training for MSHA Part 46 is allowed.
Can Safety Training Required by OSHA Satisfy MSHA Part 46 Training Requirements?
In short–yes.
According to 46.4(c), “You may substitute, as applicable, health and safety training required by the Occupational Safety and Health Administration (OSHA), or other federal or state agencies to meet requirements under this part.”
Of course, as 46.4(c) goes on to say, “This training must be relevant to training subjects required in this part.” So you can’t just give any OSHA-based safety training and then say it applies to MSHA’s Part 46 requirements.
And finally, even if it OSHA-based safety training, if you’re going to use it as part of your MSHA Part 46 Training Plan, you’ll have to document it in the terms required by MSHA in 46.9 (which we’ll discuss soon).
Check out our collection of general health and safety online training courses.
Can Employee Health and Safety Meetings Help Satisfy MSHA Part 46 Training Requirements?
Yes. According to Part 46.4(e), “Employee health and safety meetings, including informal health and safety talks and instruction, may be credited under this part.”
That’s true, at least, for the following training programs:
- New Miner Training Program
- Newly Hired Miner Training Program
- Annual Refresher Training Program
(Note that Part 46 DOESN’T say it’s ok to apply this training time for New Task Training Programs or for Site-Specific Hazard Awareness Training Program).
As we learned about OSHA training earlier, if you’re going to use health and safety meetings as part of your Part 46 Training Plan, you’ve still got to document each session in according with Part 46.9, Records of Training. In addition, when you’re recording the amount of training during one of these meetings, only include the portion of the session actually spent in training-discussions about families, the weekend, sports, and donuts don’t count.
Records of Training for MSHA Part 46 Training
OSHA requires that you create records of training on a form call the 5000-23 OR on a similar form that “on a form that contains the information listed” below [46.9(a and b)]:
- The printed full name of the person trained
- The type of training
- The duration of the training
- The date the training was received
- The name of the competent person who provided the training
- The name of the mine or independent contractor, MSHA mine identification number or independent contractor identification number, and location of training (if an institution, the name and address of the institution)
- The statement, “False certification is punishable under §110(a) and (f) of the Federal Mine Safety and Health Act,” printed in bold letters and in a conspicuous manner
- A statement signed by the person designated in the MSHA-approved training plan for the mine as responsible for health and safety training, that states “I certify that the above training has been completed.”
When Must Records of Training Be Made for Training in Different MSHA Part 46 Training Programs?
You must make records of training at times times depending on which Training Program is being satisfied. Here’s the key information:
For New Miner Training Program
The training within the New Miner Training Program has three different delivery and recording deadlines, as listed below:
- For training delivered to meet 46.5(b) requirements, no later than when the miner begins work
- For training delivered to meet 46.5(c) requirements, no later than 60 calendar days after the miner begins work at the mine
- For training delivered to meet 46.5(d) requirements, no later than 90 calendar days after the miner begins work at the mine
For Newly Hired Miner Training Program
The training within the Newly Hired Experienced Miner Training Program has two different delivery and recording deadlines, as listed below:
- For training delivered to meet 46.6(b) requirements, no later than when the miner begins work
- For training delivered to meet 46.6(c) requirements, no later than 60 calendar days after the miner begins work at the mine
For New Task Training Programs
Records of training for New Task Training programs must be created upon completion of the new task training [46.9(c)(3)].
For Annual Refresher Training Programs
Records of training for the Annual Refresher Training Program must be created “after each session of annual refresher training under 46.8” [46.9(c)(4)].
For Site-Specific Hazard Awareness Training Programs
Records of training for Site-Specific Hazard Awareness Training Programs must be created upon completion by miners of site-specific hazard awareness training under §46.11 [46.9(c)(5)].
But there’s a special exemption in Part 46 that applies to this requirement. Here’s what 46.9(i) has to say (pay special attention to the bold letters): “You are not required to make records under this section of site-specific hazard awareness training you provide under §46.11 of this part to persons who are not miners under §46.2. However, you must be able to provide evidence to us, upon request, that the training was provided, such as the training materials that are used; copies of written information distributed to persons upon their arrival at the mine; or visitor log books that indicate that training has been provided.”
Since the definition of “miner” as defined in 46.2 is key here, let’s review that [46.2(g)(1-2)].
Miner means:
(i) Any person, including any operator or supervisor, who works at a mine and who is engaged in mining operations. This definition includes independent contractors and employees of independent contractors who are engaged in mining operations; and
(ii) Any construction worker who is exposed to hazards of mining operations.
(2) The definition of “miner” does not include scientific workers; delivery workers; customers (including commercial over-the-road truck drivers); vendors; or visitors. This definition also does not include maintenance or service workers who do not work at a mine site for frequent or extended periods.
You may find this article on MSHA Part 46 Training for Non-Mining Employees helpful here.
Maintaining Records of MSHA Part 46 Training
So how long do you have to keep these records of training, you ask?
According to 46.9(h), you’ll have to keep most copies of training certificates and training records during his or her employment AND for at least 60 calendar days after a miner terminates employment.
An exception here is that you only have to keep records and certificates of annual refresher training under 46.8 for two years.
As you might have guessed, MSHA will want to be able to view your records of training. As explained in 46.9(g), “You must make available at the mine a copy of each miner’s training records and certificates for inspection by us and for examination by miners and their representatives. If training certificates are not maintained at the mine, you must be able to provide the certificates upon request by us, miners, or their representatives.”
Finally, you’ve also got to give miners a copy of their training records and certificates when they leave your employment [46.9(f)].
You may find this article about MSHA Part 46 Recordkeeping helpful as well.
Paying Miners for Training
Basically, you’ve got to provide training during work hours and you’ve got to give miners normal pay for completing the training.
In addition, if the training involves travel, you’ve got to pick up the bill.
Here’s how 46.10 puts it:
(a) Training must be conducted during normal working hours. Persons required to receive training must be paid at a rate of pay that corresponds to the rate of pay they would have received had they been performing their normal work tasks.
(b) If training is given at a location other than the normal place of work, persons required to receive such training must be compensated for the additional costs, including mileage, meals, and lodging, they may incur in attending such training sessions.
Contractors and MSHA Part 46 Training
Because it’s common for contractors to work at a mine site, the question arises: “Who is responsible for providing Part 46 training to contractors?”
Let’s break it down into two categories to see who’s responsible for what. First, the production-operator:
- Has the “primary responsibility for ensuring that site-specific hazard awareness training is given to employees of independent contractors who are required to receive such training under 46.11 of this part.”
- “Must provide information to each independent contractor who employs a person at the mine on site-specific mine hazards and the obligation of the contractor to comply with our (MSHA’s Part 46) regulations, including the requirements of this part.”
And next, the independent contractor who employs a miner:
“Each independent contractor who employs a miner, as defined in 46.2, at the mine has primary responsibility for complying with 46.3 through 46.10 of this part, including providing new miner training, newly hired experienced miner training, new task training, and annual refresher training.”
“The independent contractor must inform the production-operator of any hazards of which the contractor is aware that may be created by the performance of the contractor’s work at the mine.”
And here’s the definition of “independent contractor” from 46.2:
Independent contractor: “Any person, partnership, corporation, subsidiary of a corporation, firm, association, or other organization that contracts to perform services at a mine under this part.”
Read this article for more information about MSHA Part 46 training for contractors.
Conclusion: What Is MSHA Part 46?
Hopefully by this time, you’re no longer asking yourself “What is Part 46?” By now we hope we’ve given you an effective overview, including getting you up to speed on each of the following:
- What is MSHA?
- What is MSHA Part 46?
- What is a Training Program?
- What are the Required MSHA Part 46 Training Programs?
- What is an MSHA Part 46 Training Plan?
- How to Keep Records of MSHA Part 46 Training–and How Long?
- And more, including contractors, compensation, and other issues
The safety training required in Part 46 is critical for keeping a safe and healthy work force at mines. And there are all sorts of reasons to comply if you’re a mine production-operator. It’s the right thing to do, there are heavy compliance penalties if you don’t, studies show a direct link between workplace safety and the financial bottom line of companies, and more.
If you’re looking for help with MSHA training, check out the following online MSHA training options and tools we’ve got for you:
- Online MSHA Part 46 New Miner and Annual Refresher Training
- Additional Online MSHA Part 46 Training Courses (New Tasks, Etc)
- Additional Online “General” Safety Training Courses
- The Convergence MSHA LMS for managing MSHA Part 46 Training, Recordkeeping, & Documentation
And did you know that our MSHA Safety Training won the ISHN Best Safety Training Award? We’re proud of it and you’ll see why.
OK, we’ll talk to you soon. Let us know if you have questions and don’t forget to download our free Guide to MSHA Training Requirements.
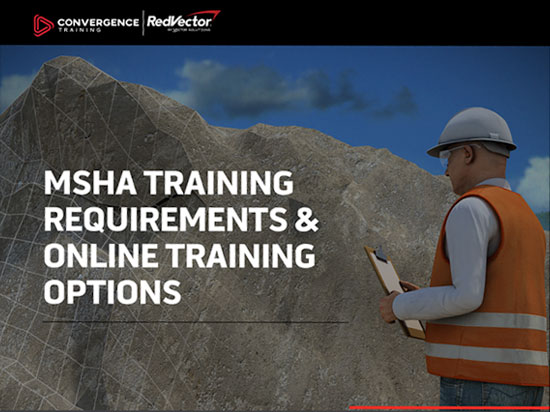
MSHA Training Guide and Online Training Tools
Download our free guide to learn about MSHA, the MSHA Part 46 and 48 training requirements, and how to use online tools to satisfy MSHA Parts 46 and 48.
Your article was very informative on MSHA training. Since MSHA was implemented, do you know how many lives were saved? Is site-specific hazard awareness required for everyone?
Alex,
I’m not sure there’s a way to determine the number of lives saved. Maybe MSHA has some stats: http://www.msha.gov/
Site-specific IS required for everyone. Read up here: http://www.ecfr.gov/cgi-bin/text-idx?SID=5870b64aaa17fd930c418d234ba8735f&node=se30.1.46_111&rgn=div8
Here’s what they say at that link:
You must provide site-specific hazard awareness training before any person specified under this section is exposed to mine hazards.
(b) You must provide site-specific hazard awareness training, as appropriate, to any person who is not a miner as defined by §46.2 of this part but is present at a mine site, including:
(1) Office or staff personnel;
(2) Scientific workers;
(3) Delivery workers;
(4) Customers, including commercial over-the-road truck drivers;
(5) Construction workers or employees of independent contractors who are not miners under §46.2 of this part;
(6) Maintenance or service workers who do not work at the mine site for frequent or extended periods; and
(7) Vendors or visitors.
(c) You must provide miners, such as drillers or blasters, who move from one mine to another mine while remaining employed by the same production-operator or independent contractor with site-specific hazard awareness training for each mine.
Hi, Jeffrey. Nice summary! I was on the NSA committee that drafted the language for this back in the day. One thing that you may want to clarify (but not required) is that you do NOT have to be an MSHA instructor, as in Part 48. As long as you are competent in the subject matter, it doesn’t require an instructor card.
On a practical note, yes, an employer can use safety meetings as part of the training but if an employer selects that method vs conducting a set-aside day for annual refresher, the employer must be able to prove that all employees received all the required training. If someone is out sick, on vacation, loading a customer, etc and misses the training and not there to sign the training roster, it is the employer’s responsibility to ensure that employee gets the training. For some larger companies, its just too much hassle to track. So, again, just to clarify, it can be done throughout the year but the employer needs to understand what that is going to entail before selecting that method.
Lastly, the operator and contractor always have to coordinate and provide site-specific hazard training to workers. That is NOT the same thing as an operator providing AR or NMT, which should only be done by the operator for its OWN employees. Contractors need to take responsibility for their employee training for NMT, AR, Task-specific training, etc. The operator should be expected to ONLY provide site-specific hazard training.
Thanks! RD
Hi, Randy,
Thanks for stopping by and leaving the comment with some expert opinion.
Agreed about an instructor not having to be approved for Part 46 (as they do for Part 48). By which I mean, I agree that you’re right. Although I really think the approval program is a good one and it should be required for Part 46 and Part 48 instructors. I know some mines go the extra distance and have their Part 46 instructors get approval, and I applaud that.
I don’t think the article suggests the approval is required for Part 46 (and I don’t think that’s what you’re suggesting), but I’ll go back and maybe add a point noting that it’s not.
By the way, have you read our interview with MSHA’s Jeff Duncan about the Instructor Training session and the approval process we’re talking about here? You might find it interesting: https://www.convergencetraining.com/blog/the-msha-instructor-training-session-an-interview-with-jeff-duncan-director-of-educational-policy-and-development-msha
Likewise, you may find this article interesting, which talks about the approval necessary for Part 48 and not necessary for Part 46: https://www.convergencetraining.com/blog/what-is-an-msha-approved-instructor-in-msha-part-48
Good point about safety meetings. Of course, ultimately that point is true of all training–even if it’s a set-aside day. What you’re really getting at, and I know you know this, is the importance of due diligence, making sure everyone gets training, and keeping proper records. We have a lot of customers use our MSHA LMS to ease recordkeeping chores this like, and they’ve reported it’s very helpful for making sure required training is complete in the way you’re talking about (including for safety meetings, but for all training). Here’s some information about that LMS if you’re interested: http://www.convergencetraining.com/msha-training-online.aspx
We also cover recordkeeping and reporting as one of the helpful aspects of having an online system to manage your MSHA safety training in this free download, which you might find interesting: https://www.convergencetraining.com/blog/online-msha-compliance-guide-download
And I think you’ve correctly stated the responsibilities for contractor training as well. We cover that in a little fuller detail in this article: https://www.convergencetraining.com/blog/msha-part-46-training-requirements-for-contractors
A quote from that article:
“The production-operator has two primary responsibilities when it comes to the employees of independent contractors who will be working at their site as miners.
•The first is that the “production-operator has primary responsibility for ensuring that site-specific hazard awareness training is given to employees of independent contractors who are required to receive such training under 46.11…”. That’s from 46.12(a)(1). You can read more about the Part 46 requirements for site-specific hazard awareness training here.
•The second is to “provide information to each independent contractor who employs a person at the mine on site-specific mine hazards and the obligation of the contractor to comply with our (‘our’ means ‘MSHA” there) regulations, including the requirements of this part.” That’s from 46.12(a)(2).”
And a second quote from same article:
“Now let’s look at the independent contractor’s responsibilities for Part 46 training for his or her workers (who are considered “miners” under 46.2).
•The independent contractor “has primary responsibility for complying with 46.3 through 46.10 of this part, including providing new miner training, newly hired experienced miner training, new task training, and annual refresher training.” That quote’s from 46.12(b)(1), and those links take you to the MSHA site that explains each of those Part 46 training programs in more detail.
•In addition, the independent contractor “must inform the production-operator of any hazards of which the contractor is aware that may be created by the performance of the contractors work at the mine.“
Note that because 46.12(b)(1) says the independent contractor is responsible for complying with 46.3-46.10, that includes creating a training plan (46.3) and keeping records of training (46.9).”
Looks like we agree on all that, as well.
Thanks again for stopping by and for the comments. Have a great Friday.