
Every company we work with says that safety is job one, safety is the most important thing, there’s no work goal that’s worth sacrificing safety, or something like that. And they’re sincere.
To that end, they come to us for help improving their safety training programs, using our 3D-animated online safety training materials, our best-in-class learning management systems for use in industrial and manufacturing companies, or even our mobile safety training and work-support solutions.
One top of that, of course, they’ve got multi-tiered safety efforts at work. They may have a safety management system; they’re using the hierarchy of controls and they’re performing proper job hazard analyses. They hold regular safety meetings, they track safety incidents and near misses, and they perform incident investigations.
So there’s a lot of serious effort going into safety and safety training.
But how do you KNOW that you’ve got a safe workplace? For many, the answer is to look at the incident rate. The goal is always zero incidents; a decreasing incident rate is a good sign, and an increasing incident rate a bad one.
But that’s not enough. There’s more to safety than just your incident rate, right? So a lot of safety people talk about leading and lagging indicators of safety.
What does that mean? Well, let’s take a step back and look at the terms leading and lagging first. Leading indicators are things that occur before an incident could occur, and lagging indicators are things that happened after an event occurred. Leading is before; lagging after. It’s the same use of the terms that you hear when people on the news are discussing economics.
That’s the new, updated, traditional safety logic. But we’re also throwing in some additional thoughts about an even newer concept called Safety Differently, which turns some of this stuff on its head as well (especially the stuff about lagging indicators). So we hope you find this article thought provoking in a safety kind of way.
- Learning Management Systems
- Online Safety and Health Training Courses
- Custom Safety Training
- Incident Management Software
- Mobile Safety Training Apps
Lagging Safety Indicators
Traditionally, safety management has focused on lagging indicators, the things that happen after incidents. These include incident rates, workmen’s compensation costs, incident-related days away from work, the OSHA 300 logs, safety-related production stoppages, and more.
You get valuable information from your lagging indicators, because they show you the real effects of your safety program in terms like cost, number of injuries, and severity of injuries.
Leading Safety Indicators
But because focusing on the past isn’t enough, safety professionals also look at leading indicators, things that happen before an incident (and that hopefully can be used to prevent incidents).
Leading indicators including things like safety training, the performance of job hazard analyses (JHAs), employee surveys, safety audits, observation of good housekeeping (or the lack of it), discipline for safety violators, and more. Some people consider near misses a leading indicator, and others a lagging indicator–you’re getting to a fine philosophical point with near misses, I guess. I see them as a leading indicator, but the opposite point has merit too.
For more about this, check out our extensive article on Leading Indicators for Safety Program Performance Evaluation.
Incident Investigations
To make best use of information about leading and lagging incidents, you need a proper safety and health management program (or system) plus some method for investigating incidents.
This article explains safety and health management for you.
The video below, from our online Incident Investigation training course, introduces incident investigations.
Safety Differently
If you attended the recent ASSE Safety 2017 conference, or if you read our overviews of each day of the conference, you may have picked up on the discussion of “safety differently” from speakers such as Ron Gantt, who led his own presentation, or talk of “human and organizational performance, or HOP” from Dr. Todd Conklin, who spoke during the plenary session.
Safety differently puts a different spin on some of this discussion, especially the focus on incidents/injuries/illnesses (which are lagging indicators).
We’re going to be exploring these more closely in the near-term future, and plan on writing about them. We also encourage you to check them out. To that end, here’s the Safety Differently blog, where you can find a lot of intriguing articles on the topic.
Or, if you can spare about 5 minutes, here’s a short video featuring Dr. Sidney Dekker talking about safety differently.
Conclusion: Leading and Lagging Incidents and Safety Measurement
So what’s the takeaway? The best way to evaluate safety at your workplace is to use both lagging and leading indicators, and maybe consider some of the lessons from the “safety differently” and “human and organizational performance” crowds.
Doing so will give you the full, big-picture view. Lagging indicators will tell you the current “cost” of your safety situation, and leading indicators will help you predict safety problems and fix them before they lead to incidents.
Want more about leading indicators for safety? Here’s our own article on leading safety indicators; here’s a nice article we found at the NSC’s Safety & Health online magazine, and here’s an interesting article on leading indicators at the Predictive Solutions blog.
We also think you might benefit from online Incident Management Software, which includes tracking capabilities for near-misses, injuries, illnesses, and other incidents (plus OSHA/MSHA recordkeeping, incident corrections, and more). The video below gives you more information about our IMS.
Acknowledgement: This post originated as a result of two separate but nearly simultaneous discussions on LinkedIn. The first discussion was prompted by a post of my own and a follow-up question from Abdil Kareem of Nippon Jordan Fertilizer Company (NJFC). Shortly after participating in that discussion, I participated in another discussion originated by Shawn Galloway of ProAct Safety, Inc. that addressed similar issues. Thanks to both those gentlemen, and the other participants in those discussions, for their thoughts and contributions. LinkedIn is a good place to learn some stuff and kick around ideas. Since then, the article has grown to include an introduction to safety differently/human and organizational performance (HOP).
Please feel free to download our free guide to conducting a Job Hazard Analysis, below.
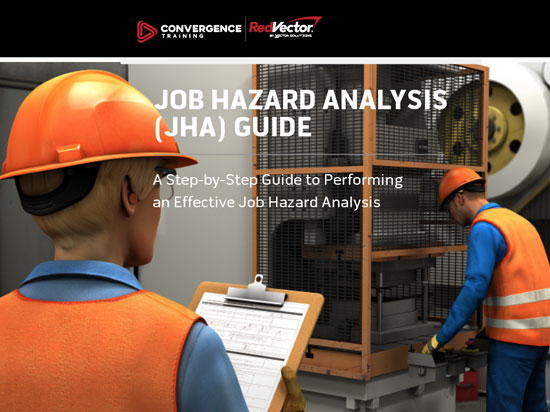
Job Hazard Analysis Guide
Learn how to perform a job hazard analysis on the job with our free step-by-step guide.
There is not a lot of leeway here. Lagging indicators are a record of what has already occurred. They can not be changed. They could be considered a record of our failures. Hense the negative connotation. Leading indicators are chosen to reflect the current state. To be effective these indicators must be appropriate to the job site or project. Inappropriate indicators do not add any value to the