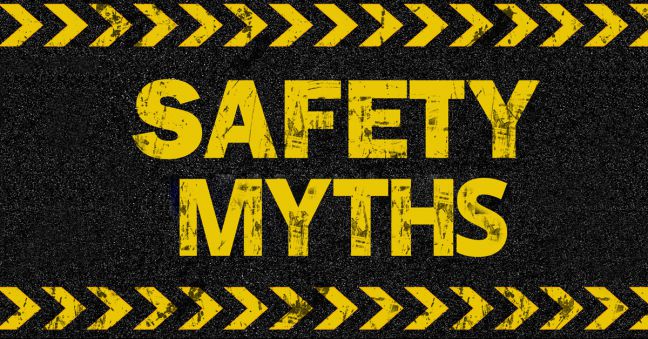
Every field has its sets of established truths. But if you consider some of these so-called “truths” a little critically, you sometime find out they’re not true at all. It’s like the professional version of an urban myth. They’re in the air around us; we read about them and we heard smart people saying they’re true; we never stop to question if they really ARE true; and ultimately, we end up believing in them ourselves.
In the learning and development field, a classic myth is that you can get better training results by designing training to match your learner’s so-called learning styles. But I digress–we’ll get back to that in another article.
In occupational safety, there may be some myths out there too. And that’s why we had the conversation below with “safety mythologist” Carsten Busch. Put on your critical-thinking cap and your skeptical socks and give it a listen (or a read). And many thanks to Carsten for his sharing his time and knowledge with us.
- Learning Management Systems
- Online Safety and Health Training Courses
- Incident Management Software
- Mobile Safety Training Apps
10 Myths about Occupational Safety
Let’s dive right into our interview with Carsten Busch…
Convergence Training:
Hi, everybody, and welcome. This is Jeff Dalto of Convergence Training back with another webcast from our webcast series. Today we’re going to be in the world of Occupational Safety and Health. And we have a pretty cool guest, I’m excited about this.
This is Carsten Busch. He’s a self-proclaimed safety mythologist, and he’s the author of a book called Safety Myth 101. And we’ll be discussing a number of the safety myths that he brought up in his book. And so before we go much further, let me just start by welcoming Carsten and saying hi.
Carsten, how you doing today?
Carsten Busch:
Thank you, Jeff, for inviting me to do this. And I’m extremely fine.
I’m looking forward to do this hour with you.
Getting to Know Carsten Busch
Convergence Training:
As am I. Well, cool. Thank you so much for coming on. And before we start getting into the prepared questions, could you tell us a little bit about yourself, how you see your role in safety or your views on safety, and show everybody that book Safety Myth 101 that we will be drawing some questions from?
Carsten Busch:
When we first showed the thing. And there’s a Dutch version if you dare, it’s even more beautiful.
Convergence Training:
I’m sure it is.
Carsten Busch:
Well, I’m not going to take that one out.
A bit about myself. I’ve worked for over 25 years now in safety, starting in occupational safety, adding some quality on the way, then moving into traffic safety. I’ve worked a lot in railroads and a bit in process safety but mostly safety management.
And for the past four years, I’ve worked for something completely different. Occupational Safety again, back to the roots, but within the Norwegian police force, I’m an advisor on occupational safety, which is an extremely interesting world to work in. Totally different from industry and railways and stuff like that.
So you asked me say something about my role in safety. And well, I proclaimed myself a safety mythologist. That was mostly for fun because nobody has a title like that, and everybody wants to be unique. So I became unique, but there’s also something more about it. I try to be critical with regard to establish truths, but also with regard to the newer stuff, and try to see what’s in it and what’s useful and well, mainly ask questions. Not give answers that much, maybe.
Are Risks and Hazards Bad?
Convergence Training:
Great, great for those listening, I think you’ll agree, like I do, Carsten is a provocative and interesting guy. He mentioned that he’s critical of traditional safety dogma but also some of the some aspects of new safety as well and Carsten, I know you’ve written an article on that, and I’ll be sure to include a link to that article, kind of showing how you position yourself, I think, to some degrees in the middle of those two camps. Also, people will find that a Carsten is pretty funny as well, something I enjoy. And with that, we’ve got a series of 10 questions prepared for Carsten, and we’ll jump right into the first one. And each of these kind of relate to a safety myth that Carsten has identified in his book.
Side note: Check out Carsten’s article Brave New World, which kind of situates him between old and new safety,
Carsten, first one: tell us about risks and hazards and are risk and hazards bad?
Carsten Busch:
Well, if you take the point of departure in our everyday speech, you would probably think they’re bad because when people talk about hazards and risk, when you run a risk of something, then most of the time it’s something bad, and hazard is often the origin of risk. And therefore we also see hazard as a bad thing. Hazard is something that can do damage to something. That’s, well, the loose definition of a hazard that is found in some standards.
But if you think about it.. really? Because look at this one (shows a coffee cup). You know what it is? A coffee cup. And I use those often when I do workshops and risk assessment courses, because it says here in small print – so you know, there’s a lawyer involved, probably: “caution contents may be hot.”
And then think about it. If you go to 7-11 or where ever you get your coffee, and you would get a cup of a nice, cold coffee, which is very safe. You’re not going to the counter and say thank you for the most safe coffee ever. You’re going to complain and you’re going to complain loudly. Because coffee has to be hot, has to be strong. I nearly want a heart attack and I want my tongue burned. Not really, but I want the possibility.
So I really want the hazard, I want the risk, and I’ve thought about—do you know the movie, The Matrix? And somewhere in that movie comes up the question, “Why have these machines built the virtual worlds the way they have built it? Because and then they explain they had a version of the world that was perfect and there was no harm whatever, but people died.
And then they created a new version of their matrix where people have problems and stress and pollution and stuff. And that’s where they thrived. And I think that that’s a really nice image for us. Because systems and organisms need risk, we need stress. We need signals to react upon, if we don’t get them, we die, we will wither away.
Convergence Training:
So I guess you’re making two arguments, I think. One is it with the hot coffee, I’m drinking one myself right now, and I’ve stolen that example from your book and I use it a conferences myself, so credit now where credit’s due. That risk brings, you know, good, bring some form of pleasure or reward or something good. So you really, I think part of what you’re saying is you can’t have that success you want in business sometimes without taking some measure of risk or confronting some level of hazard.
And then secondarily, I think you’re saying they act as an indicator or a signal that something bad is about to happen. Am I getting both those right?
Carsten Busch:
Yeah. I should say we need risk in order to develop, to learn, to…whatever. But maybe not too much, and certain risks we don’t want.
Is the Definition of Safety “The Absence of Incidents?”
Convergence Training:
So next question. And this has to do ultimately with the definition of safety, which is something you hear discussed quite a bit lately.
A lot of people will say that safety is the absence of incidents, I believe, some organization or some standard and maybe you know this off the top of your head, has defined safety as such, or as something similar. But what is your take on that? Is safety the absence of incidents?
Carsten Busch:
I don’t think so. But if you go out on the street and you ask people “What is safety for you,” most people will probably return something in the line of not having accidents, or they say, well, it’s a feeling, feeling good or something. I think that are the two most common general answers and the connection to accidents is very natural.
And if you go back in the history of safety, all the early writers or most of the early writers write about accident prevention, like Heinrich, who of course is the best known guy, his book was Industrial Accident Prevention. And there were several books of that title, not only by him but also by others.
Safety and risk only enter the language later on, not as promptly as accident prevention. So I think it’s quite natural of the people identify the two together safety and absence of incidents. And the thing is, of course, to test if the definitions works. Say you would have to re verse it and say “If I don’t have an accident, am I safe?”
And one of the examples I use is when I go into a bathtub, and I think let me be a bit efficient and blow dry my hair, which is very hypothetical, of course, and I get out of the box, and nothing has happened. Was that safe? Of course not. I’m doing something very, very dangerous sitting with an electrical appliance in the bathtub. But when I get out, one could say, well, this was safe because no accident happened. No it’s not. It’s lethally dangerous but I was lucky.
Convergence Training:
So, not defining safety as something like the lack of incidents would lead you to practice and measure safety differently, is that correct?
Carsten Busch:
I think viewing safety as an absence of accidents can give you some degree of information. It can be a measure. But it’s a very weak measure, and it’s only a very gross, rough approximation. You will have to look at other things to get a better picture.
Like how do we deal with people and hazards, for example, and risks? Well, how are the barriers and stuff like that?
Convergence Training:
Great, great. So some measure of information in your incident rate, but that’s not the full story.
Carsten Busch:
It’s not the full story. And then you can even expand on that and say, well, depending on your definition of safety, you might even say that accidents are part of safety. Because if you talk about acceptable risk—engineers have that kind of definition of safety, an acceptable level of risk. That means you will accept some kind of accident. And then accidents are actually part of your definition of safety, which is kind of upside down thinking for most people, I guess.
Convergence Training:
Yeah, yeah. Could you maybe talk a little bit more about that? That’s pretty intriguing. That upside down world of thinking before we move on to the next question?
Carsten Busch:
Yeah. Well, if you use something like ALARP where you work, as low as reasonably possible, which means you can make a decision. You’re going to accept some kind of level and then you have to show that in some way, you have barriers, etc. to prevent this as much as possible, but not at any cost. You’re not going for zero but you’re going for something above zero without maybe spelling it out.
The thing is, I think that most people even though you have to this assessment where you say “We are going to accept some measure of risk, because we cannot afford or we don’t want to afford absolute safety, and it’s impossible anyway.” But when an accident happens, funnily enough, people suddenly expect the absolute anyway. Or they want some, even higher because they believe that the fact that an accident happened proves that you were not safety.
Well, that’s not necessarily so, because probably you were or maybe you were within the margin. Maybe you weren’t because those assessments may be faulty. So you don’t know.
And that’s probably—and now I’m really thinking out loud—there is probably another reason why defining safety as an absence of accidents is not a good measure of safety because it doesn’t say necessarily something about the processes that went on before. Maybe you did very good assessments, maybe you did put in place every measure that was possible or necessary or reasonable. But then something totally unpredictable happens or something happens that everybody thought would not happen. This is a one-in-a-million; you hear always the one in a million chance. Maybe this is the one in 1,000,000, and one in a million is maybe acceptable.
So then now, yeah, accidents do happen.
I’m not sure if I made any sense now, because I was mostly thinking out loud, and this was not rehearsed in any way.
Convergence Training:
No, I think you did. I mean, it ultimately, it seems like you’re coming down to the fact that, in risk thought we talk about as low as reasonably possible, which suggests that we’re willing to live with a certain amount of risk, and that suggests we’re willing to live with a certain amount of injuries. Maybe they’re minor injuries, or maybe there’s such major outliers that are so unlikely to occur, that we’re willing to live with that risk and the potential because most the time, it’s not going to happen. Is. That about right.
Carsten Busch:
Yeah, that sums it up pretty nicely.
Are All Accidents Preventable?
Convergence Training:
All right. Well, I guess, leading nicely from that, our next question was, are all accidents preventable? And I’m guessing, you’re going to say no.
Carsten Busch:
Yeah, we’ve discussed that a bit already, and I’ve a couple of problems with that statement. It’s a very known slogan, of course, and there are some major players in safety that will promote it. And I think the thought behind it is probably good, but the wording is totally wrong.
Firstly, it’s usually applied in hindsight. In hindsight, you can say “Oh, well, we could have prevented this. Because if we had such and so and something different, then it would not have happened.” The problem is, of course, prevention is something proactive and not in hindsight. So there’s a little mismatch there.
But then you can also think, what is actually necessary to make this true to prevent all accidents? And then you need quite a lot of stuff, you need unlimited information about what you’re doing, about what you’re going to do. You need 100% prediction, you need unlimited resources. And I don’t think any organization has any of these three thing—100% knowledge, prediction and resources. And you also can’t have any surprises. I think it’s that’s totally not the world we are living in.
So, it’s just not possible. If the people who use the slogan “All accidents are preventable,” are trying say is possibly every accident is an opportunity to learn and improve, and that I can fully agree upon.
Let’s put it that way then—all accidents are an opportunity to learn. That I think is a much better way of looking at things than saying it’s preventable, because then you are in quickly in the role of saying “Okay, we didn’t prevent so you’re more in the negative mood, I think then, and it’s I think it’s one of the points that Todd Conklin makes in…not his last book. I haven’t read that one, what’s it called? The serious accident prevention book about two years ago now.
Convergence Training:
Oh, the one about preventing fatalities?
Side note: Check out Todd Conklin’s book Workplace Fatalities: Failure to Predict and our own article about Dr. Conklin’s book on preventing fatalities at work. Also, Pam Walaski makes this same point in our recent interview Using Risk Management to Reduce SIFs at Work.
Carsten Busch:
Yeah, that one. He says quite a lot about getting away from the prevention thinking. And I think that’s the same, that I’m arguing against the idea that all accidents are preventable. If you think that way, you will be in a much more negative view than if you didn’t, if you say well, there’s some opportunity to learn from accidents.
Can Safety Pros Find THE Cause of an Incident?
Convergence Training:
All right, so we’ll take that up again and go a little further into that in the next question. It’s kind of interesting. It’s the second time you’ve argued against the kind of simplistic safety slogans. We talked about things like zero harm, not being an attainable cause or goal and also about the slogan that all accidents are preventable. Also being a little simplified and maybe not great. And in particular with all accidents are preventable, you mentioned that that is said retro-actively, not in a forward-thinking manner. And I wondered, that leads nicely to our next question, which ultimately, I think has to do with root cause analysis and similar efforts.
And that leads actually our next question, which is, can safety pros identify the cause? Can you talk to us a little bit about causality and the difficulty in identifying the cause of a workplace incident?
Carsten Busch:
Sure. It’s one of the things I must say I have learned over the two and a half decades that I’ve been in in safety. Because when I started and I don’t know how it was for you, I’d been told taught in many accident investigations courses, your job is to find causes. So it just sticks in your mind. An accident happened, we have to find the cause, discover the cause. And a few years ago, and I don’t know what ticked it off, I started thinking about that and reading a bit. And then I entered a whole discussion of constructivism. And causes—they are not things. The cause is something we construct in our heads. Constructs are things that don’t really exist because you don’t find causes in the natural world. But we attribute cause with something that happens.
Take for example, I bumped into a glass door and, oh yeah, I wasn’t paying attention. I construct that cause. But I could also construct a lot of other causes. Like I was distracted by my colleague who called me and I turned my head and bang, walked into the door; or the guy who designed the door and didn’t do his job, because he should have put these things on door to make the glass more visible for people walking towards the door.
So you see, I have a couple of choices to make and maybe all of them apply at the same time.
So THE cause–I don’t really believe in it. And it has of course also to do with your stop rule–where you going to stop your analysis? Are you going to stop at the first convenient point where you think “Hey, I can solve this problem? Then I could stop with me I walk out the door and I have to pay attention. So I am the cause and I should shape up and not be distracted and not look at my iPhone and whatever.” Or are we going to analyze further and look at the bigger system with distractors and the design of the door and, is my workload too high so that I need to check my phone to see where my next appointment is? Etc, etc.
So if you want to find the cause, it’s probably just you choosing something and it’s not the truth then. It’s a version of a truth, I think.
Convergence Training:
And so I’d imagine there are probably a couple of issues with selecting the cause. One is that it’s often a multifactorial thing; two, as you’re saying, within those multiple factors or causes, you wind up pretty randomly or arbitrarily selecting one, usually, or sometimes at least kind of the simplest one. And that’s going to leave you I think, amongst other things, vulnerable to making decisions based on well-known cognitive biases, amongst other things, of the type that maybe Daniel Kahneman would have written about in Thinking, Fast and Slow. Does that sound about right?
Carsten Busch:
Yeah, definitely. And mostly, if I walk into the door, I’m not going to blame myself. That’s a fundamental attribution error. If I make a mistake, it’s everybody else’s fault. But if you walk in the door, stupid, Jeff again.
Are People the Problem?
Convergence Training:
That’s a good example. So the exact same thing, two different causes, depending on whether or not I was involved.
So that leads us nicely to our next question. We have the stop point, the simple answer, the cognitive biases. What would you say if I told you that, or many people will tell you, that people are the problem, people and human error ends up being identified often as the root cause of many incidents? What’s your response to that?
Carsten Busch:
Well, sometimes they are, probably, because people make mistakes. And of course, you can choose to stop there. And for organizations, it’s often a solution to a problem. And it’s a very cynical solution, but it’s a reality we should be aware of. For an organization, it’s a solution to, figuratively speaking, throw somebody under the bus and then move on.
But if you want to really solve a problem, I think James Reason was one of the first to say the people in the sharp end just inherit the problems from higher up in the system or elsewhere in the system. And that is how it often is that people are placed into a situation where they are almost required to make a wrong choice, because you have time pressure and you have to be safe and you have to deliver quality and within budget. And within all these constraints: faster, better, cheaper. The old NASA slogan, you’ve probably seen the memes on the Internet–pick two because you can’t get all three. So you can have fast and cheap, but that’s probably not good.
So, yeah, sure, people will screw up in one way or the other, but is that because of them? Sometimes maybe. But often it’s a function of the situation they’re placed into. And so one of the really, really, really important things I’ve learned in the last years is that your reflex shouldn’t be to ask, “Why did he do something stupid like that?” But instead, try to make a reflex of asking, “Why did it make sense to him or her in that situation?” And asking that question will lead to where we’re past the point where the people are the problem to finding your answers by people are in a problem. And then you have the people as the starting point or the error is the starting point and not as an answer.
What To Think About Heinrich’s Pyramid?
Convergence Training:
Great. So this next question gives us an opportunity to kind of pull in at least three threads we’ve already talked about. You’ve already mentioned, Heinrich, we’ve already discussed whether or not people are the problem, and that’s going to lead to a discussion of the 1-29-300 rule, and we’ve already talked about causation.
And I wondered, Heinrich’s Safety Pyramid is kind of a much-discussed, hotly debated issue in safety these days. And this concept that there’s a 1-29-300 rule within that pyramid, and that there’s some kind of causal relationship between the incidents at the bottom, the less severe incidents at the bottom, and the more severe incidents at the top. And I wonder if you can just kind of ground us in a discussion of Heinrich’s Pyramid and give us give us your views on that—what Heinrich actually meant, what lessons we can take from it today, and so on.
Carsten Busch:
I think we need to expand this webinar now from an hour to four hours.
Convergence Training:
OK….the abbreviated version.
Carsten Busch:
And I really need some more preparation, but the pyramid I think is probably the most misunderstood, misquoted, and….well, often it comes out totally wrong. Because there are many misunderstandings and they’re just copied and repeated and enhanced in many ways.
If you, for me, boil down the message from Heinrich’s Pyramid, it’s about opportunity. If something little happens, you do not have to wait till it becomes something bigger. If you can act now, it was an argument for proactive safety, safety management, or accident prevention as he called it, and he says several places in his texts, a lot of attention is given if something major happens, if something is really bad, if someone is really badly hurt, if somebody is killed. If a factory blows up, we are going to investigate and put a lot of effort into it and then try to prevent it.
But why don’t we look at the precursors of things that happen? And I think that’s a good thought. Because I don’t have to drive with my car with worn tires. And when my tire blows up and I end up in the ditch, that’s not the moment I’m going to change my tire. I do regular checks. I see well now the profile is really low. I’m going to get new tires. And then well, I’ve possibly–that’s the thing, you never know if you actually prevented anything, because you can say this didn’t happen, so a good score. I’m going to count everything I’ve prevented. That’s rain dancing. And so as I say, I’ve possibly prevented a car crash. I don’t have to wait until the big thing happened.
The problem is that people have misunderstood the whole message and then mash everything together, all the slips, trips and falls and the bumping heads and the cuts in fingers, etc. and think if you do something about the small accidents, you will prevent the Deepwater Horizon from blowing up. It doesn’t work that way, of course.
Because you have to stick within similar events. If I changed my tires, it doesn’t prevent me from experiencing brake failure. That’s a different scenario. And the thing that Heinrich did with this 1:29:300 ratio is he averages a lot of different accidents. But in his examples, he discusses similar events like somebody crossing a rail track at the point where he shouldn’t cross them and he does this several thousand times and then he gets hit by a train. I think that was one of his examples. Well, there is some thousand to one ratio and then he has another thing which has a 200 to one ratio, and then he averages them and comes up with this total number. The problem is many organization have just worked with a total pyramid and think “Well, we do something about frequent stuff, and then the infrequent stuff goes away,” but it doesn’t work that way. It works only if you are working within your sliver of the pyramid, which is similar to the top, which is kind of what about the people in safety discuss about the serious incidents and fatalities (SIF)? They’re moving that way. But I think they’re still mashing stuff together. Which doesn’t work. It’s better than looking at the whole pyramid, but it’s not entirely there.
But the main message, I think, is forget the ratio, because it doesn’t work. Instead think in terms of opportunities.
The problem is, of course, how do you know what opportunities to use? Because you can’t react to them all. For example, I think a lot of maintenance works on the basis that is similar to Heinrich’s Pyramid. You see small stuff, like a low profile on my tires, when do you react on it? When is it critical enough to do something before it becomes something bigger? Or, maybe it’s just a vibration in my steering wheel. It can be some totally random thing. It can also mean that my tires aren’t balanced anymore. And those are two big problems I think in applying the thought. I think the thought is very good. It’s about opportunity, being proactive. Don’t wait till somebody dies or gets hurt, you can do this much earlier at lower costs, and you have more of these opportunities. The problem is you can’t take them all, so which one to pick? And how to separate them from the everyday stuff.
Convergence Training:
Can I ask you a couple follow ups on that one?
Carsten Busch:
Yeah.
Convergence Training:
The first one being, if I don’t have resources to react to everything at the bottom of the pyramid, and I have to separate the signal from the noise as you talked about, and ideally identify something that at the bottom that is truly a precursor of something that could lead to the top as opposed to just something that’s going to stay at the bottom, if you will, any tips on how to identify that signal from noise, how to how to recognize this as a precursor?
Carsten Busch:
One thing that’s also recommended in the literature I’ve read on serious injuries and fatalities is criticality or potential in this case. If I cut my finger in the kitchen, in a worst one in a billion case, it can of course become a blood infection and I can die. But it’s not very likely.
But me using the same kitchen knife to repair electrical appliances in my home–yeah, that’s a higher potential there. I think it’s a silly example, but it’s the one I’ve got.
So that’s one way and the other. And I think it was Andrew Hale, who wrote, in my opinion, the best paper so far on the triangle in 2000 or 2002. It’s free online, downloadable. He speaks about looking at the amount of energy in any case, I think.
Side note: You can download Andrew Hale’s Conditions of Occurrence of Major and Minor Accidents: Urban Myths, Deviations, and Accident Scenarios here.
And well, that’s probably quite a useful and simple way of looking at the matter. If you think again of Deepwater Horizon, or Texas City, where, where the investigation showed they had misapplied and misunderstood the triangle, and Andrew Hopkins has written about this, among others. Slips, trips and falls don’t have the same amount of energies in them as high tower filled with explosive liquid.
Side note: See Andrew Hopkins, Failure to Learn.
So that should be a signal that okay, maybe you should do a bit less about the slips, trips and falls and maybe a bit more about the process safety stuff in the refinery or whatever.
Convergence Training:
Great so criticality and energy and if I could ask you two kind of specific questions about Heinrich’s Pyramid because I know that along with being a safety mythologist, to my mind the biggest safety archivist I know, I’m always seeing you on LinkedIn with a picture of the late copy you just got of a different old version of a book by Heinrich or somebody. And I know your book Safety Myth 101 addresses this as well. I think one of the things that led, I think you make this one as well, one of the things that led or contributed to the misunderstanding or this kind of simplified misunderstanding of Heinrich’s Pyramid is simply the manner in which it was visually depicted in successive volumes of the book.
If I’m correct that this is a point you made, and its’ not just something I read elsewhere, could you kind of explain that to us briefly?
Carsten Busch:
Well, one thing…it’s both the genius of Heinrich and partly also, his curse, the curse of his success. He was absolutely brilliant in coming up with things that are very sticky to our minds.
Side note: Read about how to make things stick.
He makes these pictures, dominos, a pyramid, and he has a couple of others, but those are the two really iconic ones and everybody in safety knows them, probably almost everybody. And then he had also a genius to apply some numbers to them, and whether they were based on actual research or if he just dreamed them up, or did some rough research and came up on something that looked like these…they’re brilliant, because once you’ve seen the numbers, you’re not going to forget them. And also they look so nice and precise. And numbers attract people, I think, “Well, this is really something 1-29-300” and then there’s this neat one plus 20 minus 30, which makes three hundred and etc.
And of course, he says in all his writings, these are averages etc. And he shows other examples where he kind of shows how he gets to the numbers. Well, he doesn’t fully explain it, but then he repeats the ratios over and over and over again. And that’s what sticks. And then people think, “Well, this is how it has to be.” And I’ve been at a meeting where someone said our ratio in our reporting system, it doesn’t correspond to Heinrich’s Pyramid, so we must be under-reporting, and I said, “Hello. You live in a modern time, you have another industry, and even Heinrich makes clear at several places where he says there will be unique ratios.” In addition, the people simplify this and say we will keep this and this is it. No, it isn’t.
Convergence Training:
In addition to the use of numbers and repetition, am I correct that in an early volume, he depicts the three levels as physically unattached. And then later volume of the book, he depicts it as a pyramid. And putting them together in a single pyramid with three levels kind of suggest a causality.
Carsten Busch:
That’s right. Yeah, the first two versions look like, well, a ziggurat, a step-like pyramid.
Convergence Training:
Yeah, yeah, that’s an issue for a different conversation. But I don’t think we often think about the importance of visual communication in safety communication, but I think that’s a great example.
Carsten Busch:
That’s one of the things we can learn from Heinrich because he’s been dead for like 60 years almost. We still talk about the stuff he found already created in the early 30s late 20s.
Side note: For even more on this topic, check out Carsten’s thesis on Heinrich’s Locale Rationality, which Carsten wrote while studying at the Lund University Department of Human Factors and System Safety (impressive!).
Are Mistakes Bad?
Convergence Training:
So several times you’ve talked about opportunities and that leads to our next question, which is: Are mistakes bad?
Carsten Busch:
They are not. When I do workshops, I have some examples that I tend to use and often I ask people, while we discuss what is error and how error is something we do in hindsight, etc. And then if you make an error, we often apply a lot of, let’s say, judgment and value to it because of its consequences. If the consequences are bad, then we say “Well, this was an error you must have been really stupid or careless or whatever,” but if the consequences are good, even if you actually make a mistake, but if the consequences are good, then you’re suddenly a genius or you think out of the box, you’re creative, etc.
And then I ask people do you know Alexander Fleming was? And well, some do. And he was a scientist, and he made a serious error because he forgot to sterilize his petri dishes or whatever he didn’t do or maybe his assistant had a day off or was sick or whatever. Then the next day he comes to his job and sees some mold growing in dishes that should be clean. And he thinks “Wow, this is interesting.” Thanks to that mistake, half of us are alive because it’s penicillin that came from that mistake. And well, there’s a lot of others.
For example this—brilliant-the Post-It. It was a total failure—they were planning to make superglue. Champagne was a mistake. Yeah, you don’t want to dis-invent that one.
And no, mistakes aren’t bad. And, of course, we can also apply this to our everyday lives for ourselves. I moved to Norway 10 years ago, from the Netherlands, and I speak quite fluent Norwegian and people are surprised. How did you learn so fast? And I think it’s mainly by making mistakes and being corrected. When I started my job, my first job in Norway, I said to my colleagues, “Don’t talk English to me. I will try to follow, and I’ll ask if I can’t.” And every time I wrote an email or letter said, “Please give me feedback on my Norwegian”. And there’s these red squiggly lines in Microsoft Word, every time I write and mistake, mistake, mistake, and I get better. So mistakes are brilliant. In a way. We just have to avoid some of the big ones.
Convergence Training:
That’s a great example. The second one about learning a third language, or maybe you have more than three, because it’s the other side of the coin of the champagne and penicillin examples. So you’ve got the first examples which are these kind of mistakes that you can dub creativity or inspiration or create an entire new opportunity. But then there’s the maybe more prosaic, humdrum, and mundane mistakes we all make at every time, but they’re learning opportunities. And the important thing is to realize it’s a mistake, because there’s a red squiggly line in your from your auto-correct, or you’re getting some form of corrective feedback from somebody who’s more experienced than you, or you’re reflecting on it, even if nobody knows the answer, and using it as a learning opportunity. Does that sound about right?
Side note: we’ve covered the importance of practicing and getting corrective feedback in this article about Anders Ericcson and deliberate practice.
Carsten Busch:
Yeah, I think we tend to undervalue these mundane learning opportunities. We get zillions of them well…not every day but…
What Is Safety Culture?
Convergence Training:
Yeah, I think that’s a great opportunity for safety professionals. And maybe you know this word, I think there’s a nice tie-in with learning organization theory, if you build in some kind of underlying process and procedure to capture those, more mundane, everyday kind of mistakes, discuss them, learn from them as a team and share that. It’s a great learning opportunity that imagine it would make a much safer workplace, but it’s, it’s probably also something that is easy to not do.
Side note: Read this introduction to learning organizations, this interview with Michelle Ockers about becoming a learning organization, this article on safety and the learning organization, or check out this webinar on integrating safety into a learning organization.
Which, I guess leads us in a way to my next question, which is about safety culture. It’s a term I hear a lot. It’s a term I hear safety professionals talk about, but it’s also a term I hear non-safety professionals talk about all the time, clearly in a way that suggests they know what it is and how to get one and I wondered if you could talk about safety culture a little bit.
Carsten Busch:
Yeah, another four-hour lecture on that. And safety culture, it’s again, one of those things that isn’t a thing. We talk about it as if it really is something, and one of my friends, he remarked at some point, the only cultures you will find in nature are fungi. So, go figure, bacteria and fungi, those have cultures, all other cultures, you can’t see. You can’t really measure but it’s something that we make up in our minds to explain what happens between people. And I think that’s a quite useful thought. That we see behavior in a group of people, and there’s something that connects them. And there are also differences between them. And that’s very important.
There are two sides with culture and we tend to focus on the thing that people have in common. People in Norway, in two weeks we have National Day, and that’s a very cultural thing. People who don’t come from Norway, they wonder “What is going on here?” People are outside then going in, in processions in the finery etc. If you come from abroad, it’s is this really cultural thing. It’s something that connects them. At the same time, people in Norway couldn’t be more different from each other than Norwegians from Frenchmen or, for example, if you take people from Oslo where I work and compare them to people from the North, 2000 miles towards the polar circle or beyond the polar circle, they are totally different people, totally different language, way of expression, etc. Which is interesting because you have a group of people, we call them regions and they have the similarities. They’re very proud of the independence and they have these traditions, etc. And at the same time, if you meet them in everyday life, well, people up north have fairly strong language, and people down south are much more careful and polite.
And you will have some the same within organizations where you try to explain the behavior then and we focus a lot on they should do the same, or act the same, or handle safety the same and then we call it the safety culture. And then we forget I think that it’s also necessary for the different parts in the organization to behave differently because the finance departments they’re probably very strict on the rules because they are audited, etc., while the maintenance guys need to be much more flexible and they need to fix things with duct tape because production has to be going to they need to get this fixed until the weekend, etc. So, you talk about one organization, but that can be very different.
And the point I was trying to make or get to is, then we try to be very normative about safety culture. You have a safety culture, if you do safety first on the agenda and you always do a task list assessment and blah, blah, blah, blah. And that’s not it. I think every organization has an organizational culture. Safety is a part of that in one way or another. And the culture that an organization has brought them where they are. So their culture has brought them to the point where they are. So their culture has helped them to be successful in some way. And that’s another reason that we should be very cautious to be judgmental about culture. But we can, of course, this is Carsten saying, well, we see things that aren’t working as they maybe should and then use the culture issue as a way of starting to discuss better or other ways to promote safety. But I I’ve been there that I’ve made some judgments about a culture but I wouldn’t do it anymore because who am I to judge what they should look like? But I can point out that things can be different.
Convergence Training:
Alright, so it’s not so simple. I guess to pick up on an earlier point about safety slogans and something you just said about organizational culture and its relation to safety culture. Can you tell it give us a few words about “safety first?”
Carsten Busch:
Yeah, that’s a typical one that is connected to the safety culture. You’re supposed to have a safety culture if you put safety first. And well, what does that mean actually, safety first?
Because then we are in the discussion, again, about what is safety. And you could of course say “Well, it means that you think before you are going to do a job, you do a risk assessment, you make sure that you have all your safety gear and you always use it, you follow all the rules, and that’s probably what most people mean with safety first. And that’s my thought, I think.
But it also ignores the messy every day that people are in. And often they don’t have safety as their first; they have safety in the back of their minds, of course, because they want to get home to family, etc. But they may have other priorities at the moment. And they probably feel that, well, we are doing well, we are quite safe now. But we have to fix this problem. Because it’s really important, helps reduce production stops. And then in hindsight, you could say “Well, you didn’t put safety first because, well, you got a serious accident and you lost some fingers and maybe they could have seen this coming.
But why did it make sense to them at that point in time? And typically people say people organizations that claim safety first with words don’t that often practice safety first in acts. And the managers, well–just look at what they are rewarded for, probably for production. And that’s good because they should. NO organization exists with the aim to be safe. Organizations exist with the aim to make product, make money, provide work to people, etc. And safety is a part of that. So safety should be integrated into all the other stuff in some kind of balance, but nonetheless, I don’t think it’s ever first. It’s just on par with the others, all the priorities.
Can We Be Funny While Talking about Safety?
Convergence Training:
Great, I’m glad you brought that back and talked about how, first, initially, safety first might mean, is it top of mind? You know, do I do it first every time as an individual employee, but also whether or not that’s truly the principal purpose for the organization to exist. And I think some organizations, some people talk about safety first in that second way. And I think that’s where it really rings hollow because it’s probably true of no organization, or very few.
Okay, one more question for you and it relates to something I enjoy about you as a speaker and a writer. Safety is very serious, and the stakes can be high. And I wondered if you could talk to us about safety and funny.
Carsten Busch:
Yeah, well I’m a big fan of Frank Zappa, and he had his famous quote, “Does humor belong in music?” And then his entire work is actually a reply to that question. And well, you can discuss his kind of humorous sometimes, but let’s transfer that to safety, and does humor belong into safety? And I think yeah, why not? And there are a couple of good reasons for it.
One of them is, things go easier if you do them with a smile. Safety has of course this picture of being serious, and following rules, and thou shalt, and that’s not really smile-inspiring, to say it mildly. So if you try to get somebody to smile while doing it, I think things get easier and you can quote the legendary Mary Poppins on that spoonful of sugar. I looked up the lyrics today and you can actually apply them to safety in a way. Yeah, I think so. We should try to make it the theme song someday.
Side note: Here are the lyrics to “A Spoonful of Sugar.” Let us know if you have thoughts on making this the official theme song for the safety industry.
But there is another side, that’s maybe even more important, because humor helps a lot to open up creativity. And I’ve been in some risk assessments and stressed in meetings and stuff, where we just spend a couple of minutes toying around with the most idiotic ideas. Which then get people laughing, hahaha, and here come even worse examples, and those tend to lead to really great ideas. Because, well, you get rid of your boundaries. You’re allowed to be silly, and then you think, hey, but there’s also this, and you can suddenly see things from another side. And that’s really, really powerful side of humor that you open up a new potential and create to use the word again new opportunities, new lines of thinking. For example, we’ve had some risk assessments where we discussed a recent movie we had seen and we discussed the scene and say well that’s a risk assessment that and how could this have played out and then suddenly, I think “Hey, when we had something similar…” and then you can play on that and get serious again, because it’s not all fun, of course. You have to have balance there too.
But I think those are the two for me to important parts of humor in safety and in work in general. There’s a famous quote, I forgot the name, “If it’s no fun, nobody’s going to do any of this.” So that’s one side and the other, which is really important I think, is that bit about creativity. It open up new potentials because you can think freely.
Convergence Training:
Right, good. So with that, Carsten, that’s the end of our questions. I thank you very much. And I wonder if you can show everybody your book again, explain where they can buy it and maybe tell them where they can find you on social media or elsewhere if they want to connect.
Carsten Busch:
This is the book, Safety Myth 101, and it’s really easy to order from Amazon. There’s a Kindle, which I don’t like. I like real books, which you can smell and, well, you can write in the Kindle, can’t you? You can highlight. You can highlight here too, and I’m sorry, there are no big margins. So, if you see my books, except the old, expensive ones, they are all scribbled full with notes and highlighted. So Amazon is a good place. You can find me, I have my own website, which I need to update a bit more often with articles and stuff. It’s MindTheRisk.com, quite easy to find, and with a logo that I stole from the London Underground, so I’m still waiting their lawyer to call me, and then I’ll change it. There’s an acceptable risk. That’s an acceptable level of risk. Yes. And you can find me on LinkedIn.
Convergence Training:
And the short videos that I’ve seen you do which I find entertaining, like, your discussion of causality that talks about Mount Vesuvius…are those at MindTheRisk.com or are they exclusively at YouTube?
Carsten Busch:
There’s a YouTube channel for MindTheRisk. I’m still learning to do that and need to do a bit more of it.
Convergence Training:
Okay. Well, thank you very much. We’d love to get you back at some point in the future. I would love to talk to you more. Specifically, I think in the book you mentioned that you’re very fascinated with risk. I’d love to talk with you more about that. And then maybe one day where you triangulate yourself between traditional safety and new safety. But that’s for future days. For everybody out there, I hope you enjoyed it, check out Carsten’s book, check out his website and his videos, it’s all good stuff. And follow him on LinkedIn where, if nothing else, you can keep up with the old safety books he’s acquiring for his collection. And have a great day.
Conclusion: Remember To Critically Evaluate Safety Doctrine & Dogma
We hope you enjoyed this conversation with Carsten Busch about safety myths, and we hope it will lead you to reconsider some truism you may have taken for granted up until now. If you’ve got any safety myths of your own to share, please use the comments section below. And don’t forget to pick up and read a copy of Carsten’s book, Safety Myth 101.
Before you go, why not download a free copy of our Effective Safety Training Guide below?
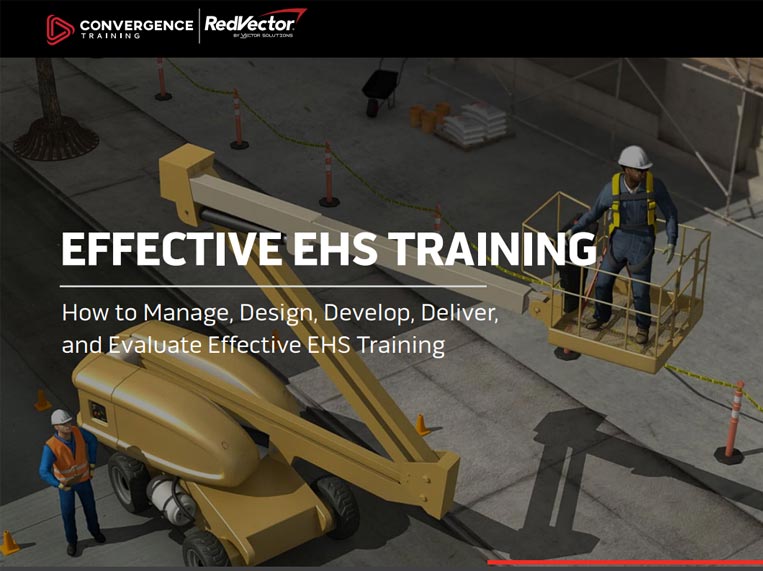
Effective EHS Training: A Step-by-Step Guide
Learn how to design, create, deliver, and evaluate effective EHS training by following these best practices with our free step-by-step guide.
Great conversation! Agree 100%
Glad you found something helpful there, Hans. That conversation with Carsten was fun. Hope to have him back again sometime soon.